
Dimple Plate in industrial process technologies
For many applications in industrial process technology, dimple plates are technically and economically advantageous over conventional heat exchangers (pipes).
Priority advantages
- Individual designs of a single and double embossed laser welded dimple plates in size, shape and material.
- Any channel design possible according to application criteria or demand for cooling and heating of industrial processes.
- Kind of weldings for dimple plates free programmable. Cut-outs for pipes, legs. etc.
- Low material costs due to the use of thin metal sheets for laser welded dimple plates.
- Less weight than half pipes for cooling and heating of industrial processes.
- No expensive double shell or half pipe construction
- Smaller quantities of heating or cooling medium due to small plate volume flows
- High heat transfer coefficient with low pressure drop
- Lower tendency for fouling
Dimple plate heat exchange panel welding contours in any shape
By manufacturing on CNC-controlled laser welding equipment, welding contours can be produced in any shape. On the one hand, this allows flexible shaping of the dimple plate. Thus, pillow plates in simple rectangular shape, can be produced just as easily as round plated or plates with complicated geometric outer contours. Cut-outs of any shape and size, e.g. for the feed-through of pipes or cables can be easily realized in this way. On the other hand, the flow arrangement for the medium in the pillow plate can also be flexibly designed by means of appropriate shape of weld seams. The flow arrangement can be easily adapted to the flow rate of the heating or cooling medium in the plate, thus optimizing heat transfer and pressure drop.
Core business of pillow-plates
Behind all the solutions we offer are our employees with their expertise. Mainly directed to process engineering, thermodynamics, fluid mechanics, pressure equipment and welding technology. We keep extensive know-how gained from decades of experience in the design and manufacture of heat transfer plates. As well as we know the specific requirements of the various industries, in which pillow-plate heat exchangers are used, and our solution can meet them to complete satisfaction. We offer engineering companies, plant manufacturers and operators from wide range of industrial sectors individual advice and precise analysis. Mainly within their heating and cooling tasks. We do focus on the aim of arriving at a solution that is optimally tailored to their needs. Both technically and economically. We support our customers in the planning, design and integration of our product into their overall system. This eliminates interfaces and the associated risks for our customers.
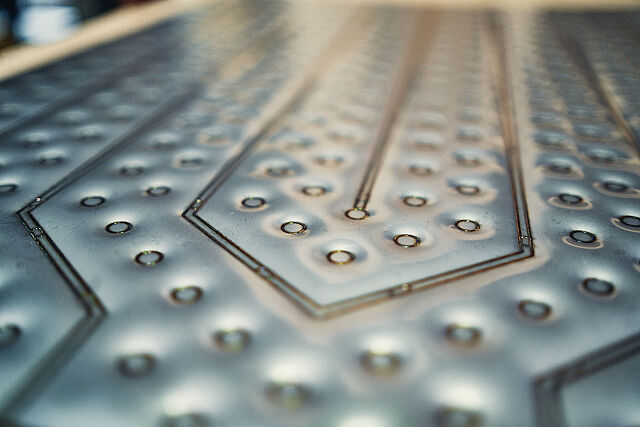
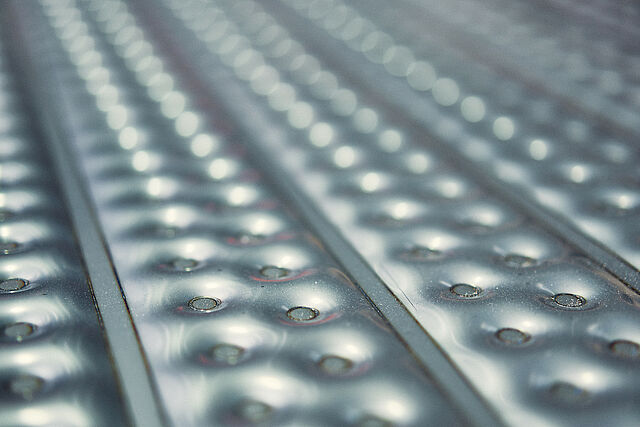
What Are Pillow Plate Heat Exchangers?
What is a Pillow Plate?
Single or double embossed dimple plates are in use for various applications. Pillow-plates profiled on one side can be used for temperature control. In general as heating or cooling of solid materials in direct contact, be it food or bulk materials. Dimple heat exchanger panels profiled on both sides, where two sheets of the same thickness are welded together, can be used in many process technology applications. For cooling or heating baths, these plates can be easily mounted directly in the bath tanks without need for complex assembly. In fluidized-bed reactors or dryers, the lower tendency to fouling and the easier cleanability proof to be advantageous. The continous heat transfer surface of the pillow plates is favorable when used as protection against thermal radiation or as flow breakers in stirred vessels. In industrial bread production in thermo-oil-heated ovens, thermal radiation from a flat heating element ensures uniform baking results.
Single embossed pillow plate in use as base plate tank wall
Individual pillow-plate heat exchangers profiled on one side can be used in a variety of ways. Not only the mentioned above. Pillow-plates profiled on one side, in which a thinner cover plate is welded to a thicker base plate can be also used to build walls or heads for tanks that need to be heated or cooled.
Laser-welded or resistance welded pillow plates and welding technologies
The production of any heat exchanger plate is mainly based on laser welding, but also on resistance welding processes. The laser welding equipment used comes from the well-known manufacturers with a lot of experience in laser welding technology, such as the market leader Trumpf GmbH + Co. KG as our main component of our laser-welding process. For decades Trumpf GmbH + Co. KG sets the standards in laser welding technology. This and the many years of experience of our welding engineers guarantee the exceptional welding quality of our pillow plates.
Pillow plates and used materials
In general, the materials used, are stainless steels as to be AISI 304 up to titanium. Stainless steel’s low thermal conductivity is partially counteracted with the ability to design thinner walls, because of its high strength and corrosion resistance. However carbon steel in the process fields, is mostly selected due to higher thermal conductivity.
Generally, the process and design execution is absolutely flexible. In focus is a very homogeneous temperature gradient, product-gentle and conciliatory tempering of products in general using liquids, refrigerant or steam as internal plate media. Even though laser welding technology is the most modern production method for dimpled surfaces, there are many applications, in which resistance welding offers technical and qualitative advantages.
Hence projects of various branches in many different industries worldwide, start with an individual consultation. Decisive for the success of the project is the professional exchange about the details and requirements of the project. Of course, this always happens in close cooperation with the user in order to work out his optimal solution.
Please note the following advantages of pillow plates:
- Individual designs of a single and double embossed laser welded pillow-plates in size, shape and material enable flexible use due to a freely programmable CNC laser welding system.
- Low material costs due to the use of thin metal sheets for laser welded pillow-plates for cooling and heating of industrial processes.
- Integration into vessels for mechanical and thermal double function with a pillow plate manufactured by laser welding.
- Very homogeneous temperature gradient, product-gentle and conciliatory tempering of products by liquids, refrigerants and steam.
- Smaller quantities of refrigerant or heating medium due to small plate volume flows of pillow-plates.
- High heat transfer coefficient with low pressure drop in case of a pillow-plate manufactured by laser welding.
- Heat transfer or radiation protection over entire surface of a laser welded dimple plate.
- Lower tendency for fouling for a laser welded dimple plate.
- Low intertia.
- Better mechanical resistance to thermal cycling with dimple plate heat exchangers.
- Long lifetime due to individually chosen materials and laser welding.
- Low production costs due to automated laser welding process for a dimple plate.
- Easy cleaning due to easily accessible single or double embossed laser welded pillow-plate prime surface.
- Reliability.
- High heat transfer coefficient with low pressure drop with these laser welded heat exchangers for cooling and heating of industrial processes.
- No expensive double shell or half pipe construction.
- Less weight than half pipes for cooling and heating of industrial processes.
- Low production costs due to automated welding processes.
- Low material costs due to the use of thin metal sheet materials.
- No surface damage on the inside of the tank due to the laser-welding process.
- No cost effective grinding or polishing of the inner surface of the tank inside due to controlled laser welding.
- Homogenous and conciliatory tempering of products using pillow plate heat exchanger for cooling and heating of industrial processes.
- Long lifetime due to individually chosen materials and laser welding.
- Laser welding contours and heat transfer freely programmable.
- Any design possible according to application criteria or demand for cooling and heating of industrial processes.
- Kind of weldings for pillow plates free programmable. Cut-outs for pipes, legs. etc.
- Integration into vessels for mechanical and thermal double function for cooling and heating of industrial processes.
- Smaller quantities of refrigerant or heating medium due to small plate flows of pillow plates
- Laser welded clamp-on plates for existing tanks for cooling and heating of industrial processes.
- Reliability of these heat exchangers
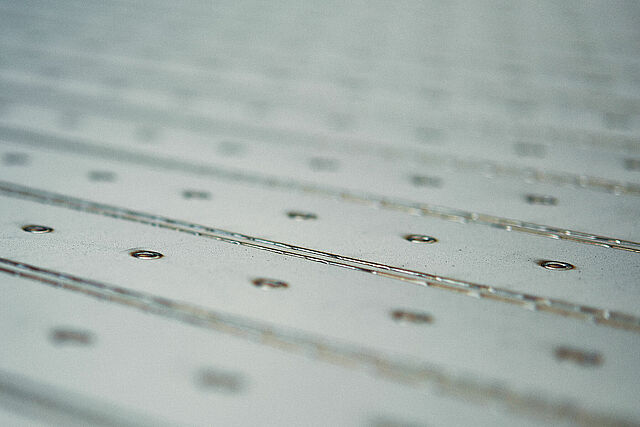
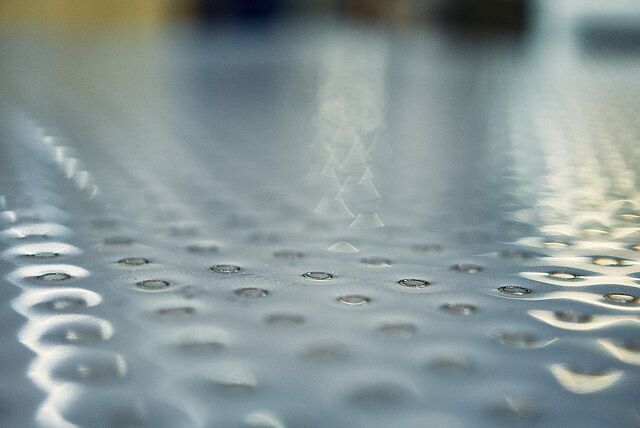
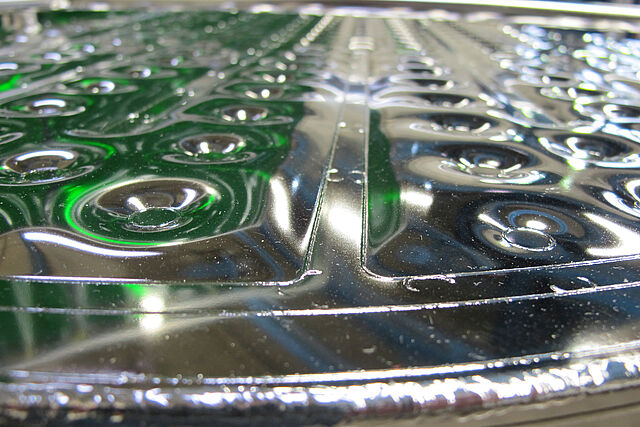
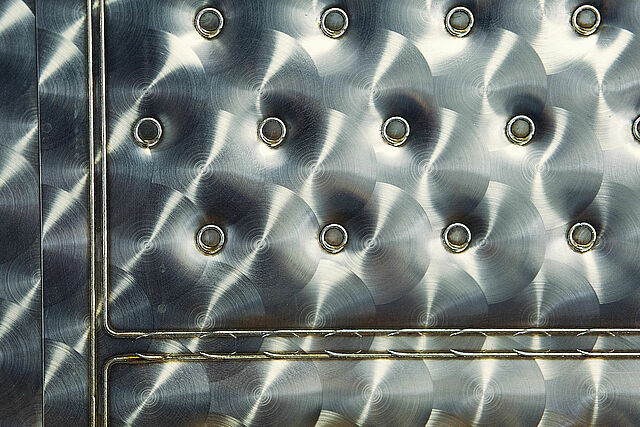