
Do you need to cool foods with high hygienic requirements as quickly as possible?
You want to cool food close to freezing? This should be done as quickly as possible and still without freezing damage?
Then the use of ice water at 0.5 ° C, so that the product never freezes and the choice of our open falling film chiller ideal or even the use of -0.5 ° C ice, manufactured by our industrial ice maker with adjustments. Our flake ice of the ice machine is optimal in the ratio heat transfer and economy. Due to the temperature close to 0°C, our chip ice has further advantages, such as round and no sharp edges and no sub-cooling (-8°C and thus freezer burn), as well as less clumping during transport or storage. The Buco chip ice machines are also variable in dimensions. Even though there are standardised dimensions, adaptation to installation in or above containers is just as feasible as other restrictions on the length, width or height of the Buco chip ice machine. We will be happy to share our experience with you in order to adapt this to your ideas.
In the comparison of flake ice (1mm thick and temperature -8°C to -10°C) and our BUCO crushed ice (chip ice 6mm to 8mm thick and temperature of about -0.5°C to -1°C), there are often subjective-visual preferences on the part of users with regard to the selection of an industrial ice maker. Customers usually prefer flake ice from a flake ice maker because it visually looks colder (whiter) and is therefore considered to be better and more effective ice. This is not the case. Ice develops its greatest heat transfer effect during melting (0°C) and thus at 335 KJ/kg (80 kcal/kg). In addition, ice near 0°C is the most economical to produce, with the lowest energy costs.
Do you have high hygiene requirements?
In applications where you have to clean the equipment once daily or even several times a day, after certain process steps, we have worked out food-safe adaptations with our customers and we recommend our open BUCOdelot falling film chiller or open BUCO ice makers with adaptations in the respective application. These include, for example, a larger plate spacing, gap-free component designs, stainless steel venturi distributers, labyrinth seals, sealing profiles, fully welded components, self-supporting housings and much more.
We will be happy to discuss the requirements of your individual process with you and advise you on our manufacturing options.
Do you need access at any time, without time-consuming assembly, without gaskets?
When using plate heat exchangers, the rubber seals of each unit must be replaced cyclically. At the moment of replacement, the unit is switched off. It is then inevitably no longer available for use in the process. This results in the so-called and unpopular downtimes.
The Buco falling film chiller can also be cleaned during operation, thus eliminating downtimes. A falling film chiller also requires neither seals to be replaced, nor suction pressure controls or any control valves. This predestines the falling film chiller as a simple and ice water cooling device, also and especially for water or process water that is charged with very small particles. The simpler the system, the more stable it is in daily use, which is why our BUCOdelot falling film chiller makes sense, as it reliably cools water to 0.5 °C without the risk of damage to the equipment due to ice build-up.
Do you use secondary refrigerants such as glycols?
Due to more extensive limitations of maximum tonnages of ammonia in the use of the respective production, there is also more and more separation of primary refrigerants (e.g. ammonia) and secondary refrigerants (glycols, or R134a/ R152a/ R404a/ R407a/ R448a/ 449a etc.). These can also be used in our open BUCOdelot falling film chillers or open BUCO ice makers with adaptations and new or other secondary refrigerants can also be simulated and calculated by our engineers. Primary and secondary circuits are spatially separated in each case in use and reference is made to a not so harmful effect on health with the secondary refrigerants in comparison to ammonia. Even though it must be emphasised at this point that especially for the refrigeration technicians in the process, ammonia with a strong odour is more of an advantage, even if it is toxic, when it comes to the detection of leaks, which can then be found and remedied more quickly.
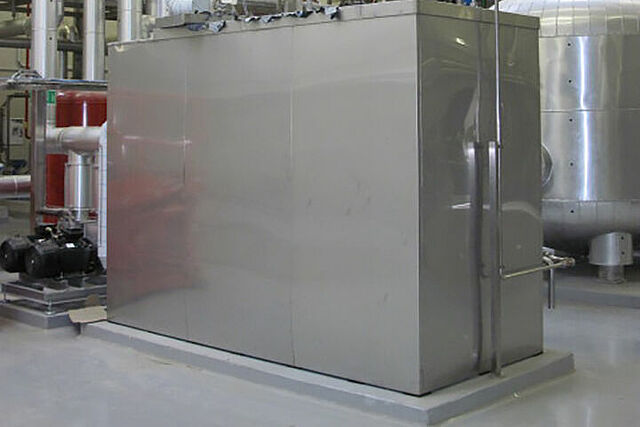
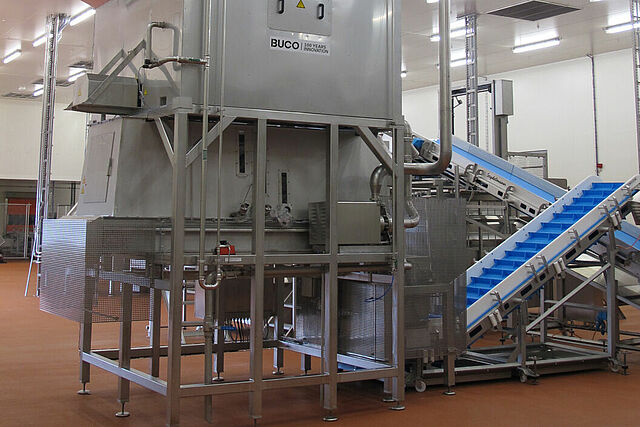