
Pillow Plate Heat Exchanger
A single or double embossed pillow plate heat exchanger often is very flexible coupled with design, surface and mechanical requirements for either heating or cooling. Especially pillow plate contents are considerably smaller than those of comparable tubular heat exchangers and dependent on the weld seam distance and the pressure height.
Dimple Plates one side flat for food contact cooling
Use of single embossed dimple plates in the application of a contact freezer plate for food, e.g. meat, fish and chocolate pralines.
It is our daily task to design and manufacture pillow plates.
- Welding contours of dimple plates freely programmable.
- Sizes DIN A5 up tp 14000mm x 2000mm
- Wall thickness from 0.6mm on 0.6mm up to 12mm
- Surfaces stained, ground, polished
- Up to 80 bar operating pressure
- Stainless steel
Priority advantages
- Individual designs of a single and double embossed laser welded dimple plates in size, shape and material.
- Any channel design possible according to application criteria or demand for cooling and heating of industrial processes.
- Kind of weldings for dimple plates free programmable. Cut-outs for pipes, legs. etc.
- Low material costs due to the use of thin metal sheets for laser welded dimple plates.
- Less weight than half pipes for cooling and heating of industrial processes.
- No expensive double shell or half pipe construction
- Smaller quantities of heating or cooling medium due to small plate volume flows
- High heat transfer coefficient with low pressure drop
- Lower tendency for fouling
Pillow-plates in heat exchangers applications?
Usually a single embossed pillow plate is mainly integrated into process tanks, bulk or pressure vessels, as well as it is integrated into cooling tables or conveyer structures, uniquely due to their one flat inside surface of the pillow plate heat exchanger.
Conversely double embossed pillow-plate heat exchangers have an unlimited access to all industries, in which cooling or heating are part of the main manufacturing process. Ordinarily a distinction is made between a pillow plate with spot patterns and those, which have a defined channel pattern.
Heat exchange surfaces are calculated due to each individual process application. Above all, the flexible design options of single and double embossed pillow plate allows tempering of products during other process steps. Although this saves a separate thermal process stage and often increases product quality. Furthermore, the large single and double embossed pillowplate heat surface ensures safe process control by controlled homogeneous temperature control.
What is a Pillow Plate?
A single or double welded pillow plate is made of two metal sheets of either a different or the same wall thickness, welded together by using laser or resistance welding. By a special inflation process, fluid channels are created between these two heat exchange plates. These plates are expanded until the desired and calculated channel height. The channel height describe the maximum space between the welded together metal sheets. All single and double embossed pillow-plate heat exchangers profiles and wall thicknesses are selected for throughput, allowable working pressure and pressure drop requirements from us as pillow plates manufacturers.
For the transfer of large amounts of heat or for a uniform temperature distribution inside a tank, it is recommended to install a double-profiled pillow plate heat exchnger directly inside the tank in the form of a heat exchange system. In tanks with agitators, the double embossed pillow plate also serve as guide surface for the flow. This contributes to the optimal mixing and to homogeneous heating or cooling.
How to select Pillow Plates?
The connecting pipe work to the single and double embossed pillow plate has to be laid in a way to ensure that tensions due to thermal and mechanical expansion will not lead to damage of the plate connections. The weight of the connecting pipe work has to be supported by suitable supports. If not included in the scope of delivery, we recommend as pillow plate manufacturers the use of expansion bends and/or expansion joints. Connection seams that have to be welded to the connections have to be carried out and checked in accordance with valid and authorized welding procedures.
Standard connections for pillow-plates
For a double embossed pillow plate heat exchanger, the standard connections can be either lateral or butt-welded. In the reinforced version, the double embossed pillow plate is drilled through on the inside and the tube welded to the plate on both sides.
The fluid connection to the single and double embossed pillow plate heat exchanger are either by flanges, welding nozzles or screw pipe connections. Please note that the projected flow direction for the heat transfer fluid has to be adhered to. In case of screw connections these should be re-tightened during operational conditions after a certain operational period. The single or double embossed dimple plate does not have any electric connection. In the meantime, however, the U-values are only negligibly affected by soiling or a deposit on the dimple plates. Similarly favorable temperature differences then result in a significantly better efficiency compared to compact external heat exchangers. At the same time, the products, especially food, are treated very gently.
Fouling, maintenance and cleanability
Problems in the stirring technology when used in agitator tanks are largely known. In general, chemical reactions in agitator vessels require heat exchange surfaces to heat or cool products. Coils are still mainly used in tanks for heat exchange, but they have enormous disadvantages with regard to fouling, cleaning and maintenance. Star-shaped heat exchange systems with double embossed pillow plates offer a lot of advantages.
On the one hand side the flow angle can be adjusted according to the medium, on the other hand, this flow breaker pillow plate heat exchanger system is at the same time a heat exchange surface. Compared to coils in combination with conventional flow breaker systems with coils, this plate version has the following advantages, such as clean, low-polluted surfaces (especially with electropolished pillow plates), small heat transfer medium quantities, optimum heat transfer, optimization of the pressure drop and adjustment of the mass flow angle. As pillow plate manufacturers, we have long experience to calculate and ensure performance.
High demands on surface finish
In galvanic industry, particularly high demands are placed on the heat exchanger with regard to material, surface finish, easy cleaning and easy interchangeability. Especially in temperature-controlled processes, the uniform and gentle heat input is important. For this reason, people today turn away from systems operated with circulating air. Although the described double embossed pillow plate plate system can also be used in this application, for example for heat exchange in sterilization ovens, drying cabinets in the pharmaceutical industry and industrial drying ovens. It guarantees absolutely even heat mass flow and low pressure drop due to large flow cross sections of the pillow plate heat exchanger.
Materials
Materials used, are mainly stainless steel as to be AISI 304 up to titanium. Stainless steel’s low thermal conductivity is partially counteracted with the ability to design thinner walls, because of its high strength and corrosion resistance. As where carbon steel in the process fields, is mostly selected due to higher thermal conductivity. Subsequently as pillow plate manufacturers, prepickled, brushed or polished metal sheets can be used.
Certifications, classifications and designs
Single and double embossed pillow plates have been designed, built and tested as a pressure equipment. Therefor they are supplied with an European Pressure Equipment Directive 97/23/EC are certified by CE labeling and a declaration of conformity. If agreed, additional certificates can be issued.
Together with the fittings (e.g. tubes with welded ends, flanges or threaded socket ends) these channels form a pressure chamber, through which a fluid will pass to transfer heat to/from the room enclosing the single or double embossed pillow plate heat exchanger. Depending on the channel cross-sections, the volume of any pillowplate varies. Please find details about the design, dimensions connections and authorized operational conditions in the drawings as well-known pillow plate manufacurers.
If the single and double embossed pi enclosing chamber are also a pressure chamber (vacuum or pressure > 0,5 bar above ambient) this has been considered in the design.
What are the advantages with Pillow-Plates?
- Individual designs of a single and double embossed pillow plate heat exchanger in size, shape and material enable flexible use due to a freely programmable CNC laser welding system.
- Low material costs due to the use of thin sheets for pillow-plates.
- Integration into vessels for mechanical and thermal doublefunction with a pillow plate.
- Very homogeneous temperature gradient, product-gentle and conciliatory tempering of products by liquids, refrigerants and steam.
- Smaller quantities of refrigerant or heating medium due to small plate volumes of pillow-plates.
- High heat transfer coefficient with low pressure drop in case of a thermoplate.
- Heat transfer or radiation protection over entire surface of a welded pillow plate.
- Lower tendency for fouling for a welded pillow plate.
- Low intertia.
- Better mechanical resistance to thermal cycling with pillow-plates.
- Long lifetime due to individually chosen materials.
- Low production costs due to automated welding process for a pillow plate.
- Easy cleaning due to easily accessible single or double embossed pillow plate prime surface.
- Reliability.
Single or double embossed pillow plate technical data
- Sizes from DIN A5 up to 14000 x 2000 mm.
- Up to 50 bar operating pressure.
- Wall thickness from 0.8/0.8 up to 3.0 / 3.0 mm with double embossed profile.
- Up to 12 mm groundplate with single embossed profile.
- Rolled dimple plates aswell.
- Surfaces: stained, ground, polished.
- Certificates according to TÜV , PED , TR CU (GOST) and ASME.
Single or double embossed pillow plate specifications
- Single and double embossed dimple plate heat exchanger for water, glycol, liquid nitrogen, thermal oil or steam.
- As a single and double embossed dimple plate evaporator for all refrigerants with pump or injection operation.
Single and double embossed pillow plate applications and benefits
- Homogeneous tempering of liquids in tanks using laser-welded dimple jacket tank walls.
- Conciliatory tempering of foods using pillow-plate heat exchangers
- Pillow-plates to control the fermentation temperature in the wine industry
- Heat transfer or heat recovery from puluted media and media with particles f.e. biomass
- Additional functions, such as flow breaker in agitator vessels, carrier platforms for fryers and dryers, container or vibrating conveyor troughs, radiation panels.
For over 50 years Pillow Plate manufacturers of BUCO single and double embossed pillow plate heat exchangers.
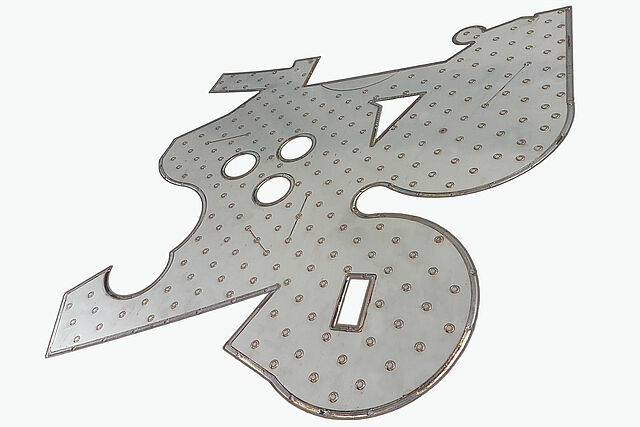
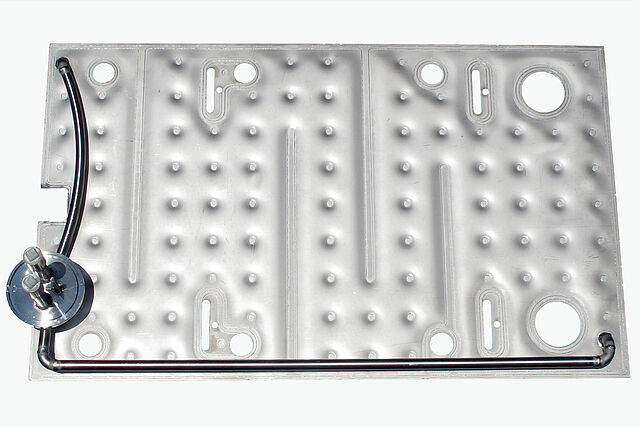
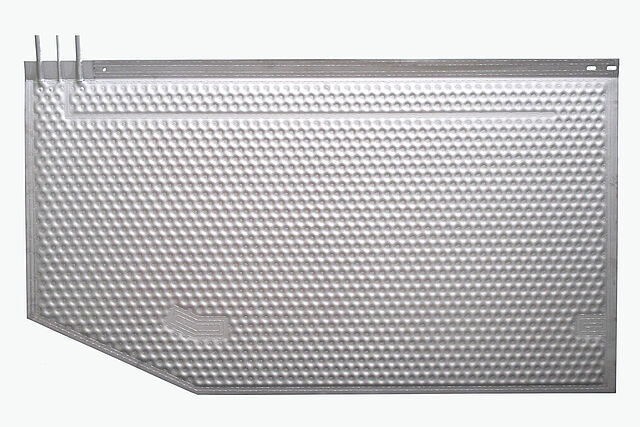
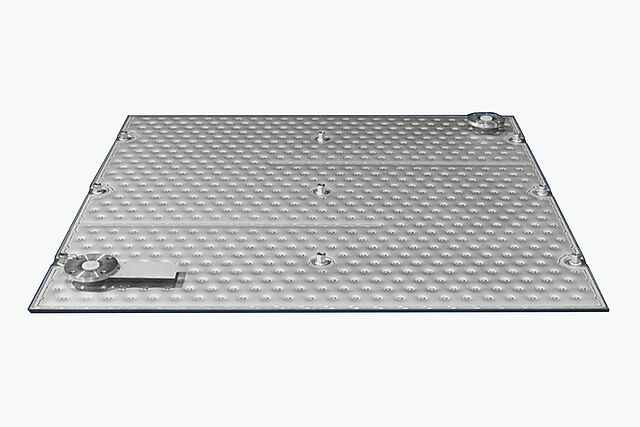
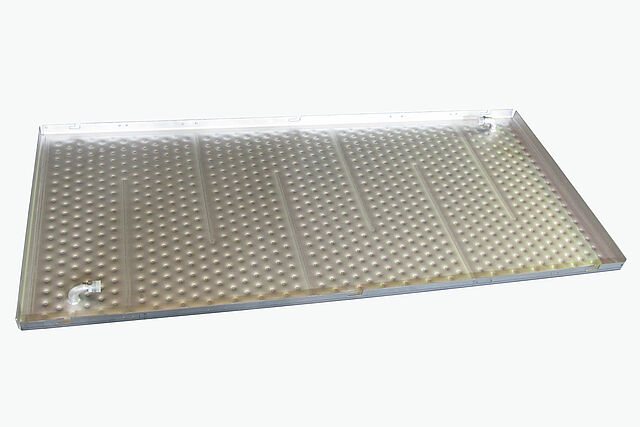
