
Pillow Plates
Product description and general properties
What Are Pillow Plate Heat Exchangers or Pillow Plates ?
The ideal flow control in the pressure chamber is the top priority for optimising the performance of the Pillow Plate Heat Exchanger (Pillow Plates) for different fluid groups. To achieve this, welds are incorporated into the spot pattern to guide the fluid through the pillow plate. The optimum combination of spot pattern and press-on height supports the best possible flow distribution by specifically influencing the flow cross-sections. This minimises dead spaces and inefficient areas in the pillow plate heat exchanger (main advantage of pillow plate heat exchanger). This efficiency is confirmed by many years of verification on test benches and customer systems, making the customised geometries of the pillow plates the most efficient on the market as main pillow plate industry manufacturer for various pillow plate heat exchanger applications.
Due to the flow within the three-dimensional pillow profile with regularly repeating changes in cross-section and direction, turbulent flows can be generated even at low Reynolds numbers, leading to relatively high internal heat transfer coefficients. Consequently, under the same conditions outside the pillow plate heat exchanger or pillow plate jacket, the heat transfer coefficient increases, and the required heat exchange area of the Pillow Plates decreases. This advantage is particularly evident when compared to tube flow in tube bundles, which are significantly less efficient due to geometric reasons. Therefore, our Pillow Plate heat exchangers or pillow plate jackets are more resource-efficient and sustainable, as the steel requirement is significantly lower than in tube solutions. Furthermore, tube, tube coil, or tube bundle solutions are highly inflexible in design, making them inferior to Pillow Plate heat exchanger systems in many applications. The mentioned heat exchange benefits apply to all the fluid groups mentioned above with individual Pillow Plates or pillow plate jackets in the assembly of complex heat exchange systems involving multiple Pillow Plates in industrial plants, a practice mastered to perfection for decades. This includes installation on existing tanks or as a structural element of a new Pillow Plates vessel as pillow plate jacket. Overall, Pillow Plate heat exchangers offer a versatile, efficient and cost-effective solution for various industrial applications. The continuous development and improvement of technology and design from us as pillow plate industry manufacturer ensures that pillow plates will remain an essential component in the process industry for years to come.
Single Embossed Pillow Plate Manufacturing Possibilities
Manufacturing options for single embossed pillow plates, such as minimum and maximum lengths and widths, connections and variable channel guides. Demonstrations of use cases.
What are the advantages of single embossed Pillow Plate Heat Exchangers?
- Individual designs of a single and double side pillow panel exchangers in size, shape and material enable flexible use due to a freely programmable CNC laser welding system.
- Low pressure loss in the shell space due to flat parallel ducts of a panel due to thin-walled plates and an automated welding process.
Double Embossed Pillow Plate Manufacturing Possibilities
Manufacturing options for double embossed pillow plates, such as minimum and maximum lengths and widths, connections and variable channel guides. Demonstrations of use cases.
What are the advantages of double embossed Pillow Plate Heat Exchangers?
- Individual designs of a double embosed pillow panel exchangers in size, shape and material enable flexible use due to a freely programmable CNC laser welding system.
- Lots of exchange surface in little space due to small thermoshelf spacing of up to 2mm clear width.
- High efficiency due to favourable flow routing (counterflow and crossflow).
Utilisation and added value of the product
What is a Pillow Plate?
Pillow panels are a fascinating engineering development that are generated using an inflation process. Two stainless steel sheets or mild steel are seamlessly welded together over the entire surface utilizing laser or resistance welding techniques. Once the sides of the plates are sealed, except for the connecting ports, the gap between the metal sheets is pressurized by hydraulic fluid, which causes the plates to undergo a forming process.
The result is the distinctive wavy surface and its custom circle weld pattern that these plates are known for. It's a remarkable process that showcases the power of modern pillow plate production technology.
When it comes to exchange panels from pillow plate manufacturers, there are two main types to consider: single-embossed and double. Although both have their applications, single embossed pillow plates are commonly used as dimple jacktes with pillow plate design as the double embossed plates are mostly used in exchanger units as exchanger plates. These plates are designed with a thicker base panel and a thinner top panel. As a result, the top panel deforms while the base panel remains unaffected. With this knowledge, pillow plate heat exchanger manufacturers can create specialized exchange panels with ease. As industries continue to strive for maximum efficiency, the use of panels has become increasingly popular. These exchangers are equipped with innovative "pillow" seam weldings, which provide targeted flow guidance in the channels of the panels. In situations where fluid velocity or distribution is a concern, these weldings can be the perfect solution. A method for obtaining flow guidance by channels. This heat transfer technology has the potential to improve the performance of exchangers even further, enabling industries to operate with greater efficiency and reduced costs.
How does a Pillow Plate Heat Exchanger work?
The connecting pipe work to the single and double plates has to be laid in a way to ensure that tensions due to thermal and mechanical expansion will not lead to damage of the pillow plate heat exchanger connections. The weight of the connecting pipe work has to be supported by suitable supports. If not included in the scope of delivery, we recommend as panel manufacturers and experts in this field, the use of expansion bends and/or expansion joints. Connection seams that have to be welded to the connections have to be carried out and checked in accordance with valid and authorized welding procedures. For the transfer of large amounts of heat or for a uniform temperature distribution inside a tank, it is recommended to install a double-profiled panels directly inside the tank in the form of an exchange system. In tanks with agitators, the double inflated panels also serve as guide surface for the flow. This contributes to the optimal mixing and to homogeneous heating or cooling. Pillow plates offer a level of reliability and durability that is difficult to match in other forms of energy transfer equipment. Their hermetic seal ensures that they can withstand demanding pressures of over 100 MPa while maintaining a high level of structural stability. What's more, their highly automated manufacturing process offers flexibility, making them ideal for a range of applications. Pillow plates can also be operated at incredibly high temperatures of up to 800 °C, making them ideal for use in even the most demanding industrial processes. As such, they have become an essential component for businesses across various industries. We have a team of experienced engineers who are experts in developing specialty engineered thermal equipment customized. If you are looking for something unique, systems that provide temperature control and uniform transfer surfaces, get in contact with us. Our commitment is to help you achieve efficient processing results, cost-effectiveness and minimal downtime.
Pillow Plate heat exchange panel welding contours in any shape
As industries continually search for new ways to optimize their processes, pillow panels or pillow plat jackets are emerging as a highly sought-after solution. Compared to traditional exchangers, they are relatively new, but their unique "pillow-shaped" of two sheets mostly nickel alloys design provides greater flexibility and efficiency in heating and cooling systems by aspect of its laser welding process. What sets them apart is their ability to serve as both panel-type exchangers and jackets for vessels. As a result, they are becoming increasingly implemented in the process industry. These exchangers represent a highly versatile and reduced deposition technology that is changing the game for many businesses. Due to their geometrical flexibility after geometrical analysis, pillow plates can be customized to almost any geometry spot welded or seam welded to offer targeted energy transfer where it is needed. Some examples are cooling of pipes in thermal processes or even battery packs and electric motors for electric vehicles in automotive industry or in falling film use cases.
Accurate thermohydraulic calculations require precise knowledge of surface area, fluid hold-up volume, cross-sectional area and hydraulic diameter designing the pillow plate heat exchanger. To obtain these geometrical parameters, researchers have proposed using Finite Element Analysis (FEM), which mimics the inflation process that occurs during the manufacturing of pillow plates. By utilizing this powerful tool, engineers can estimate theoretical burst pressures of pillow plates with greater accuracy. As a result, FEM is becoming an increasingly valuable method for those in the thermohydraulic industry who need to calculate critical parameters for optimal system design.
CNC-controlled laser welding equipment enables us to produce these mostly laser welded pillow plate with a variety of shapes, from the simplest rectangular ones to more complex contours. Thanks to this technology we can now create cut-outs in any shape and size for pipelines or cables' feed. Additionally, it allows us flexible flow design adapted to heat transfer rate and pressure drop optimization.
With their unique design, pillow plates offer a promising alternative to conventional exchanger plates. However, their thermohydraulic performance remains relatively unexplored, leading to limited knowledge and experience with their design. In response to this challenge, the industry is actively pursuing the development of commercial software tools that will facilitate research on pillow plates. If successful, such tools could unlock new possibilities for this innovative technology, making it more widely accessible and beneficial for a range of industrial applications.
Technical properties
Materials
Materials used, are mainly stainless steel as to be AISI 304 up to titanium in the pillow plate production. Stainless steel pillow plates low thermal conductivity is partially counteracted with the ability to design significantly lower thinner walls, because of its high strength and corrosion resistance in use of fastening points. As where carbon steel in the process fields, is mostly selected due to higher thermal conductivity. Subsequently as pillow plates manufacturers, prepickled, brushed or polished metal can be used.
Certifications, classifications and designs
Single and double sided pillow plates or pillow plate jackets have been designed, built and tested as a pressure equipment. Therefor they are supplied with an European Pressure Equipment Directive 97/23/EC are certified by CE labeling and a declaration of conformity. If agreed, additional certificates can be issued.
Together with the fittings (e.g. tubes with ends, flanges or threaded socket ends) these channels form a pressure chamber, through which a fluid will pass to transfer heat to/from the room enclosing the single or double pillow plates. Depending on the channel cross-sections, the volume of any pillowplate varies. Please find details about the design, dimensions connections and authorized operational conditions in the drawings as well-known pillow plate manufacturers. We are in thermal sciences, food industry and dimple jackets.
If the single and double panel of two sheets enclosing chamber are also a pressure chamber (vacuum or pressure > 0,5 bar above ambient) this has been considered in the design.
What are the advantages with Pillow Plates?
-
Individual designs of a single and double inflated pillow panel heat exchanger in size, shape and material enable flexible use due to a freely programmable CNC welding laser system.
-
Low material costs due to the use of thin sheets for pillow-plates.
-
Integration into vessels for mechanical and thermal doublefunction with a pillow plate.
-
Very homogeneous temperature gradient heat exchange, product-gentle and conciliatory tempering of products by liquids, refrigerants and gases.
-
Smaller quantities of refrigerant or heating medium due to small panel volumes of pillowplates.
-
High heat transfer coefficients with low pressure drop in case of a thermoplate.
-
Heat transfer or radiation protection over entire surface of panels.
-
Lower tendency for fouling for panels.
-
Low intertia, high turbulence, low volume.
-
Better mechanical resistance to thermal cycling and higher turbulence with panels.
-
Long lifetime due to individually chosen materials.
-
Low production costs due to automated welding process for a panel.
-
Easy cleaning due to easily accessible single or two side embossed pillow plate prime surface.
Single or double embossed pillow plates' technical data
-
Sizes from DIN A5 up to 14000 mm x 2000 mm.
-
Up to 50 bar operating pressure.
-
Wall thickness from 0.8/0.8 up to 3.0 / 3.0 mm with double embossed pillow plates' profile.
-
Up to 12 mm groundplate with single embossed profile from a laser welding machine
-
Rolled dimple plates aswell.
Single or double embossed pillow plate specifications
-
Single and double embossed laser welded panel for water, glycol, liquid nitrogen, thermal oil or gas.
-
As a single and double embossed laser welded dimple plate evaporator for all refrigerants with pump or injection operation.
Single and double embossed pillow plate applications and benefits
- Homogeneous tempering of liquids in tanks using laser-welded dimple jacket tank walls.
- Conciliatory tempering of foods using pillow-plate heat exchangers
- Pillow-plates to control the fermentation temperature in the wine industry
- Heat transfer or recovery from puluted media and media with particles f.e. biomass
- Additional functions, such as flow breaker in agitator vessels, carrier platforms for fryers and dryers, container or vibrating conveyor troughs, radiation panels.
For over 50 years Pillow Plate manufacturers of BUCO single and double embossed pillow plate heat exchangers.
Photos & examples
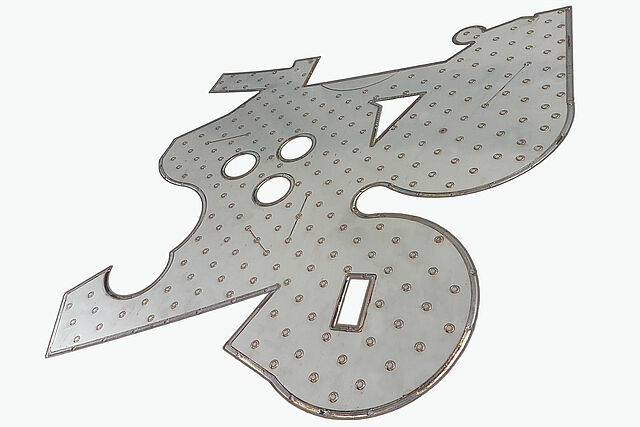
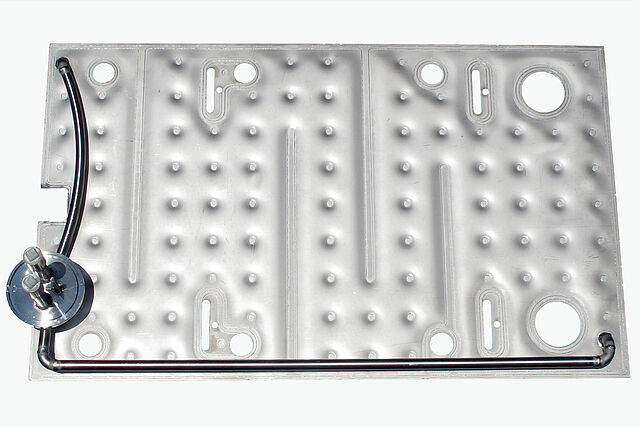
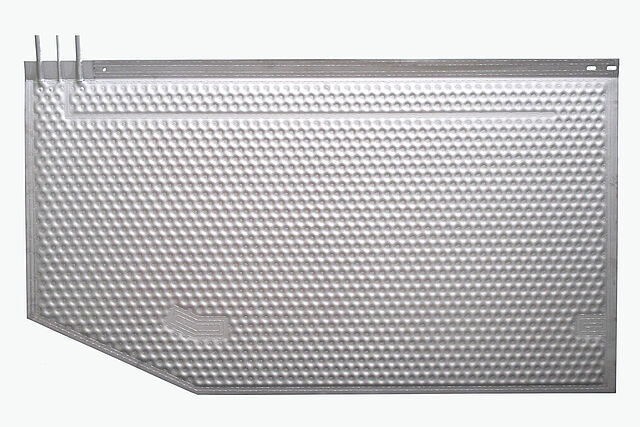
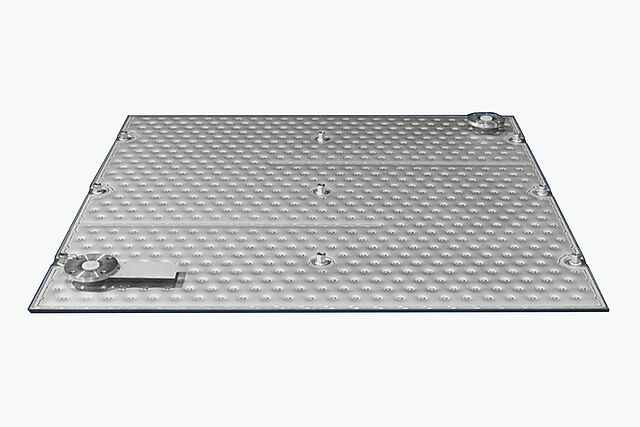
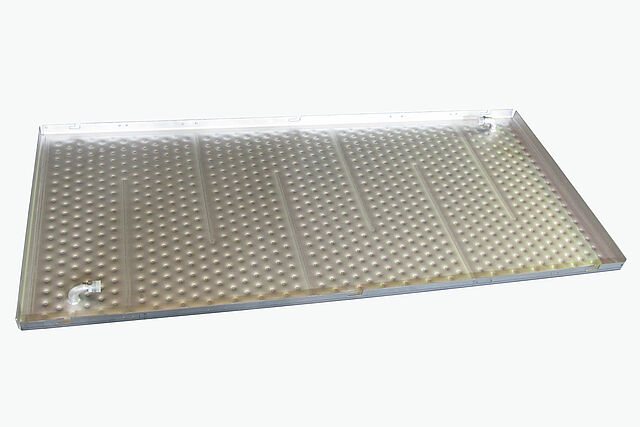
