
Distinctive cooling load peaks due to water quantity or temperatures?
Ice silos make it possible to significantly reduce investment costs, since cooling systems no longer have to be designed according to the load peaks, but the design is calculated on the average demand. The additional cost of an ice bank silo is compensated by the savings in the overall refrigeration system. An ice bank silo is recommended, because it compensates peak loads with a multiple of its cooling capacity of the refrigeration system.
Our ice water systems are more efficient than the coil-in-tank ice water systems available on the market. If the old, existing coil-in-tank ice-water systems also only worked with T0= -12°C, it is possible to get about 30% more power out of the compressor with the same compressor and direct cooling by means of a falling film chiller at T0= -2°C. The energy consumption of the compressor motors, however, only increases by 5%. Therefore, the existing motors can often continue to be used. Only the evaporative condensers that are predominantly used today have to be enlarged.
In the past, many food processing plants used coil-in-tank systems immersed in a container of water as ice storage for the ice water systems. The entire day's output was stored in ice on the pipes and defrosted when needed. Peak loads are thus absorbed. Nowadays, the process looks different. There is usually a constant base load over 24 hours plus one or two longer operating phases with high power demand. Coil ice storages have the disadvantage of the large space requirement, the low evaporation temperature (T0= 10°C to T0= -15°C) and the large refrigerant content. The heat transfer coefficient (U-value) of these systems is very low and decreases further as the ice layer on the pipe grows thicker.
In steps of optimising ice water systems, a combination of direct cooling and ice storage in one system is designed today. A combination of direct cooling by means of falling film chillers and ice production by means of ice silos is a proven and more energy-efficient solution. Depending on the space available on site, both rectangular tanks and cylindrical silos with a small space requirement can be used An alternative combination of direct cooling by means of a falling film chiller and ice production by means of ice storage is also a proven and more energy-efficient solution by building a trickle film cooler on top of existing ice storage tanks as a precooler to increase the capacity of the ice water plant. The main part of the load profile (kWh per hour over a 24-hour day) is gradually handled by the activated and deactivated falling film chiller, which is more energy-efficient. Only the peak loads are met by the ice storage or ice silo, which is also operated more favourably (T0= -8°C) than a conventional pipe coil ice storage (T0= -10°C to -15°C).
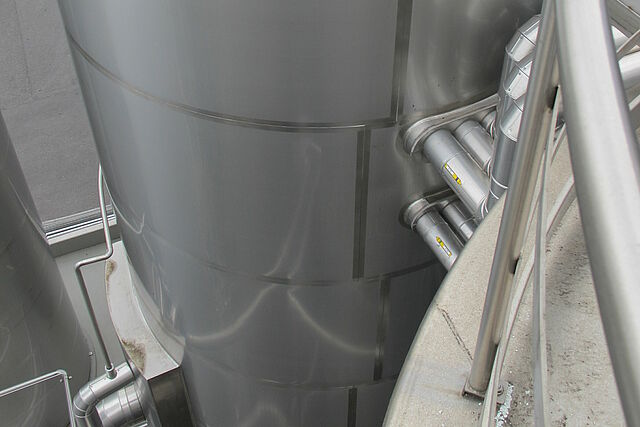
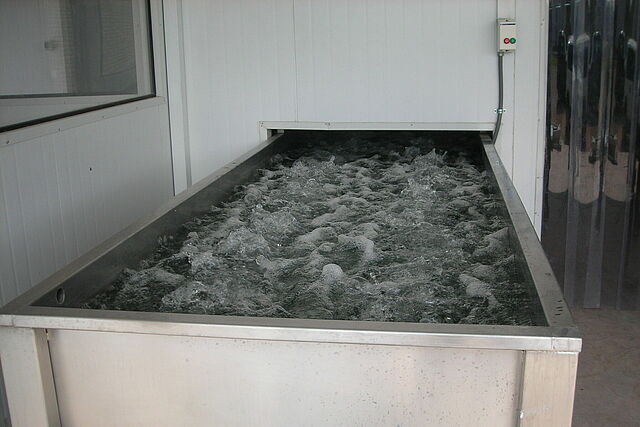