
Falling Film Chiller
Product description and general properties
Falling Film Chiller Process reliability to produce constant cooling of ice water near freezing point
Falling Film Chiller (short FFC) or so-called baudelot ice water cooler (short baudelot) are mainly designed for ice water systems down to 0.5°C near freezing point. Especially water (near 0°C) has a very good heat capacity, i.e. by contrast with other cooling agents, relatively small quantities can convey a large amount of heat. What makes them so interesting is its relatively simple and relieble operation including a high cooling performance to represent the ideal industrial chiller. Water flows down the vertical plates. It is an open system that is accessible for cleaning, even during operation. Completley made out of stainless steel.
What are the advantages with Falling Film Chillers?
-
No risk of freezing with ice water of 0.5 °C and destruction of the aparatus
-
Water chiller with low cost per kWh, High efficiency & low pressure drop
-
High heat transfer coefficients
-
Simplicity of control
-
Fully welded, no spare parts such as seals in this industrial water cooling chiller
-
Easy access to the open system water film chiller and easy to clean even during operation
-
Suitable chiller for contaminated liquids (for example greywater or red water)
-
Low tendency to fouling
-
Water film chiller completely made of stainless steel, also for salt water
Utilisation and added value of the product
Why a Water Chiller?
Furthermore water near freezing point at 0.5°C is an important part in food refrigeration, to ensure the fastest possible cooling of the product due to the best possible product quality. The open, non-pressurized water side of this Falling Film Chiller or baudelot ice water cooler allows inspections and cleaning of dirt without disassembly in a few minutes. There are no additional costs for planning, piping, mounting of the valves and electric wiring, as well as setting and programming of controllers, like known with Plate-Heat-Exchangers. No gaskets.
Most noteworthy water at desired temperature of 0.5°C can cool large quantities in very short period of time. Similarly blanching, cooling and washing processes are mainly focussed as well as mixing processes with any requirement of low temperatures while or right after mixing processes. There are various detailed sanitary adjustments for the standard Falling Film Chiller due to different process requirements in use. But the appropriate adaptation can be just as good, as the information, given by the customer, concerning the application on site aswell to cool large quantities of produce.
Industries where the Falling Film Chiller is used
What’s a Falling Film Chiller?
How does a Falling Film Chiller work?
The Falling Film Chiller or so-called baudelot water cooler consists of a distribution tray for the water at the top, a heat exchange system, a frame and a cover and a bottom collecting tank for water (optional). Water is pumped into the distribution tray and at a controlled rate is distributed homogeneously by a distribution through onto vertical pillow plates in an open system.
The process water flows in a thin film over the outer surface down on the pillow plates and obtains the highest possible outside film coefficient and cools water. By highest descent speed, highest U transmission coefficients are reached for ice water production. In order to avoid building of ice at the panels, the suction gas pressure at the evaporator suction header has to be regulated. To keep the evaporation temperature not lower than the designed one, e. g. -3°C, as well as the water temperatures and flow. At systems used with e. g. glycole inside, the glycol inlet temperature has to be controlled. Nowadays, an FFC chiller cools water and they are mostly used in combination with plate heat exchangers in dairies. Due to hygiene regulations, there is a strict separation between a closed water circuit using a primary refrigerant (such as ammonia or refrigerants like R449A, R448A, R407C, R407F, R410A, Propane, C3H8 or CO2) as cooling medium and a closed milk circuit using a plate heat exchanger. In contrast, the use of a primary refrigerant has even shifted towards the use of secondary refrigerants (glycols, brines, etc.) as cooling medium. For example, recent market trends indicate an increased preference for primary refrigerants due to better cost-effectiveness, or even the environmentally friendly option of an ecological refrigerant (CO2) as cooling medium.
A high flow velocity ensures highly efficient heat transfer and a kind of a helpful self cleaning effect, which allows the operation with polluted liquids as well. Completely made out of stainless steel, it assures all required sanitary requirements, as the water is always in contact with stainless steel parts AISI 304 or 316L or higher stainless steel grades up to titanium. An industrial chiller consists of essential components including compressors, condensers, expansion valves, and evaporators. The process operates as follows: The compressor compresses the refrigerant gas, increasing its pressure and temperature. The high-pressure and high-temperature refrigerant gas then flows to the condenser, where it releases heat and condenses into liquid. The liquid high-pressure refrigerant passes through the expansion valve to decrease its pressure and temperature. The resulting substance flows to the evaporator, where it absorbs the heat from the water to be cooled. This heat transfer occurs as the water passes through a falling film chiller. The chilled water circulates back to the application (process) that needs to be cooled. The low-pressure and low-temperature refrigerant gas then returns to the compressor. The cycle can be repeated as needed.
Comparison of Falling Film Chillers and Plate Heat Exchangers
If you are an engineer looking for the most efficient and effective process cooling solutions of water near freezing point of 0,5°C, then you should consider the advantages of a falling film chiller versus a plate heat exchanger. This type of chiller offers some very distinct benefits when compared to plate heat exchangers and could be just what your application needs. We'll explore how each type of solution works, discuss the various pros and cons associated with both types of chillers, and provide advice on making the best choice for your project. By examining all of these elements, you'll gain a better understanding as to why falling-film technology may be preferable over traditional heat exchangers in certain projects. The Falling Film Chiller is a specialized engineering solution, designed with Plates arranged side-by-side in an efficient frame. As the interior of each plate undergoes evaporation with ammonia or refrigerant, water streams down along the exterior to create thin films for heat exchange - enabling temperatures near freezing point and optimized efficiency far beyond HVAC applications. With precisely spaced plates at 50/150mm apart from one another complemented by 0.5/0.4 mm thick fluid layers transitionally descending downwards – this product ensures successful thermal energy transfer without fail. The FILM CHILLER, a widely-employed technological solution for businesses in both the food and beverage industry as well as chemical and pharmaceutical sectors abroad, relies on optimized film layer thickness to achieve better exchange coefficients. A thinner falling film is associated with higher levels of efficiency while increased plate numbers will result in thicker layers that reduce overall performance.
The simplicity of a Falling film chiller with open design to produce water at 0,5°C
-
Fully welded, no spare parts such as seals.
-
Easy access to this open system chiller and easy to clean even during operation.
-
Falling-Film-Chillers need mainly shut valves on suction and liquid.
-
Suitable chiller for contaminated liquids (for example greywater or red water)
-
Low tendency to fouling.
In direct contrast to the Plate Heat Exchanger:
-
Need seals to be exchanged periodically.
-
For cleaning, the unit must be stopped and dismantled. This costs time and interrupts the production process.
-
Hot gas-defrost and flow control on the water side, costs for the controllers and temperature sensors do not depend on the capacity.
-
Additional costs incurred due to the planning, piping, mounting of valves and electric wiring as well as setting and programming of the controller.
-
Contaminated media in the inner channels of the plates, especially in the pathes, pose a major problem of ice formation and mechanical destruction of the entire apparatus.
To give you an idea of the difference to a Plate Heat Exchanger, here is an excerpt from a manual of a well-known Plate Heat Exchanger manufacturer:
“Despite all mentioned advantages of Plate Heat Exchanger, it has to be told, that the Plate Heat Exchanger ice water productionn calls plant needs special control features and a careful operation (according to the water temperature near freezing point). It has to be secured, that the water temperature on the waterside of the plates never undergoes 0.5 °C. Suction pressure control is recommended. The suction pressure regulator has to have an accuracy of 0.25 °C (at the cold water probe). A regulation valve is necessary.” In conclusion, these chillers require temperature control, hot gas-defrost and flow control on the water side. The costs for the controllers and temperature sensors do not depend on the capacity while control valves, pilot valves as well as solenoid valves and shut valves are dependent on capacity. Having said that it should be taken into account that there could be enormous additional costs incurred due to the planning, piping, mounting of valves and electric wiring as well as setting and programming of the controller. PHE's have gaskets between plates likely needing cleaning depending on various water qualities causing massive loss of power if overlooked. For further guidance, please get in touch with our engineers who are ready to offer personalized advice tailored specifically to your requirements for your next 0,5°C water project.
Technical properties
Falling Film Chiller advantages
-
No risk of freezing with ice water of 0.5 ° C
-
Water chiller with low cost per kWh
-
High efficiency, low pressure drop of this water chiller, low evaporation temperature
-
Suitable chiller for contaminated liquids (for example greywater or red water)
-
Easy to clean industrial cooling chiller
-
Cleaning during operation possible with this water chiller
-
Low tendency to fouling chiller
-
No seals in this industrial water cooling chiller
-
No destruction of the apparatus in case of ice formation of this industrial water chiller
-
Special falling film chiller versions as ice water chillers possible
What are Industrial Water Chillers?
Falling-Film Chiller characteristics
-
Industrial water chiller for capacities from 10 kW to 10,000 kW
-
Evaporator for all primary refrigerants (NH3, freons like R449A,R448A,R407C,R407F,R410A, Propane, C3H8 or CO2) and operating modes. As well as secondary refrigerants (Any type of Glycol) or for brine operation
-
All stainless steel materials, from AISI304 up to titanium, 254-SMO, Duplex etc. This stainless steel execution gives assurance that the chilled water is always and only in contact with stainless steeel parts and can be used directly for the use required
-
Plug-in units up to 100 kW, or for on-site refrigeration systems
Which industrial applications need a chiller?
Falling-Film Chiller applications
-
Industrial water chiller for water cooling down to 0.5°C.
-
Fastest cooling chiller of food close to freezing by high efficiency
-
No risk of freezing damage to food used in fresh produce, meat, fish, seafood etc.
-
Falling Film Chiller are preferred in application of high capacities with limited ground space
-
Falling Film Chiller plates chill liquids to almost refrigerant temperature
- Ideal for cooling down milk on farms, dairy cooling and dairy products like yoghurt and cheese cooling. As well as for beer, bread dough, pasta, fish, seafood, fruit and vegetables as well as for food and beverages in general
-
"White Water" chiller for the cooling of vacuum pumps in the pulp and paper industry
-
Waste water chiller from sewage treatment in laundries and public swimming pools
-
Waste chiller for process and chemical industry plants
-
Cooling water for the chemical and process industry
-
Sea and river chiller in heat recovery plants or heat pumps
-
CO2 evaporation in breweries and soft drink producers
Simple Falling-Film Chiller maintenance
-
Comfortable access to the open system
-
Easy to clean:
-
open water distribution tray
-
large discharge opening for the discharge of particles
-
removable side panels
-
open construction plate system
-
Falling Film Chiller construction and dimensions example
Typical dimensions without tank
L (m) / B (m) / H (m)
Compact system: 1.2 / 0.5 / 1.8
System type A: 2.0 / 2.1 / 2.0
System type B: 3.8 / 2.5 / 2.0
Photos & examples
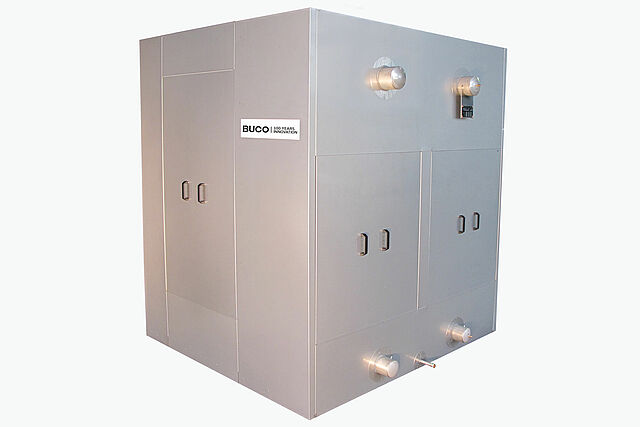
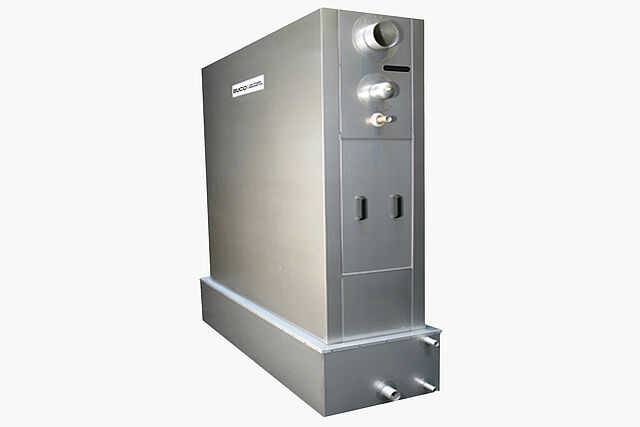
Frequently asked questions
A falling film chiller, also known as a trickle chiller, is a water chiller based on pillow plate technology. With this device, ice water temperatures below 0.5 degrees can be realized.
In a falling film chiller, water is pumped into an upper distribution tray and distributed homogeneously onto an open system of vertical heat exchanger plates, down which it runs. This device is known as a high-efficiency sprinkler chiller.
Falling film chillers offer several advantages:
- No risk of freezing and destruction of the appliance when producing ice water of 0.5 °C
- Low cost per kWh, high efficiency and low pressure loss
- Fully welded, no spare parts such as gaskets for plate heat exchangers
- Easy access as it is an open system, cleaning also possible during operation
- Made entirely of stainless steel
- Suitable for contaminated liquids, including salt water
Falling film chillers are used in various industries, in particular
- Food and beverage industry (e.g. for cooling milk)
- Vegetable processing (for blanching)
- Construction industry (for mixing concrete)
- Low susceptibility to contamination
Compared to other cooling systems, such as plate heat exchangers, a Falling Film Chiller offers the following differences:
- Fully welded, no spare parts such as gaskets
- Easy access to the open system and easy cleaning, even during operation
- Suitable for contaminated liquids (e.g. gray water or dirty water)
- Low susceptibility to contamination
Falling Film Chillers are constructed with precisely arranged pillow plates at a distance of 50/150 mm from each other. The liquid layers, which flow continuously downwards, have a thickness of 0.5/0.4 mm. This design ensures efficient heat energy exchange